PVC pipes have clear environmental advantages
Recent peer-reviewed research underscores the significant environmental advantages of PVC pipes over traditional materials, particularly in terms of their carbon footprint. For sewer pipes, PVC outperforms reinforced concrete and ductile iron by approximately 45% and 35%, respectively. This significant reduction in carbon footprint is attributed to PVC's lighter weight, which not only requires less energy for production but also minimises the greenhouse gas (GHG) emissions associated with transport and installation.
Research from Australia confirms that PVC pipes require less energy than alternatives. In all scenarios, virtually all the various forms of PVC pipes consume less energy than any other piping material. The analysis encompasses the energy consumed by all of the processes associated with the production of a building, from the mining and processing of natural resources to manufacturing, transport, and product delivery.
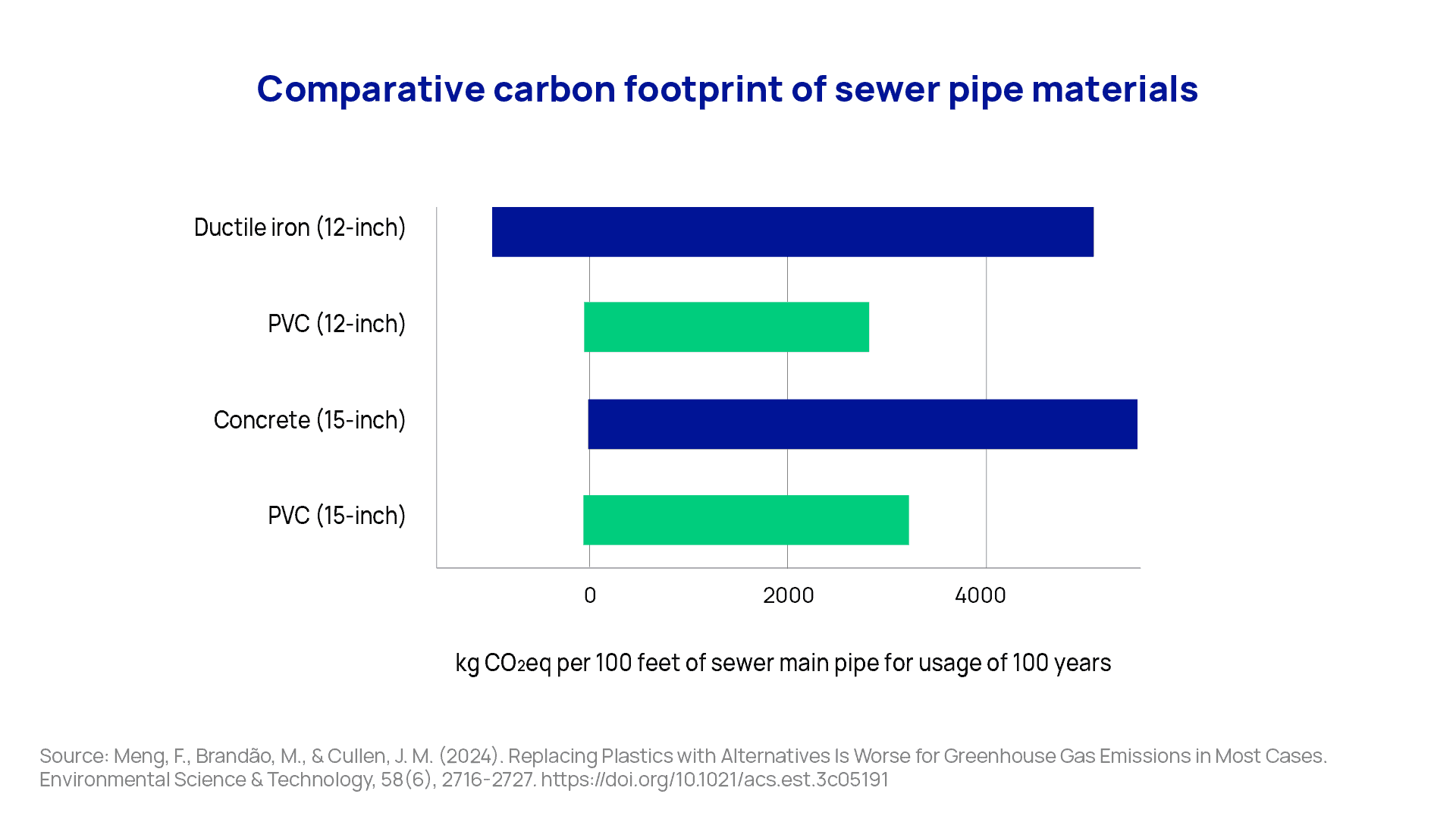

Favourable Life Cycle Assessments for PVC pipes compared to non-plastic materials
Independent comparative Life Cycle Assessments (LCAs) document that PVC pipes have the lowest environmental impact in a number of piping applications. The LCAs have been conducted by the Flemish Institute for Technological Research (VITO) and critically reviewed by the Austrian sustainability consultancy Denkstatt for the European Plastic Pipe and Fittings Association (TEPPFA). The LCAs comply with the EN 15804, ISO 14040 and ISO 14044 standards.
LCA – a life cycle approach
Life Cycle Assessment (LCA) is a quantitative and objective method to evaluate environmental loads – consumption of material and energy resources, emission of environmental load substances and wastes – through all phases of a product. This includes resource extraction, production, use and waste disposal. For LCAs to be accurate they must follow strict ISO standards.
Four key reasons to use LCAs
By using LCAs correctly it can be ensured that:

Product systems are not erroneously favoured or condemned on the basis of individual results

Developments do not inadvertently shift or even increase environmental impact but in fact reduce it

The resources available are directed in such as way that they achieve the greatest environment benefit for the entire system

PVC product systems have been investigated using LCA methodology in almost all significant application areas in terms of production quantity
Eco-profiles and Environmental Product Declarations for PVC
The Environmental Product Declarations (EPD) for PVC resin are based upon life cycle inventory (LCI) data from Plastics Europe’s Eco-profile programme. The Eco-profile and EPD represents the average industrial production of both vinyl chloride monomer (VCM) and polyvinyl chloride (PVC) from cradle to gate. The Eco-profiles and EPDs for VCM and PVC were fully updated in 2022.
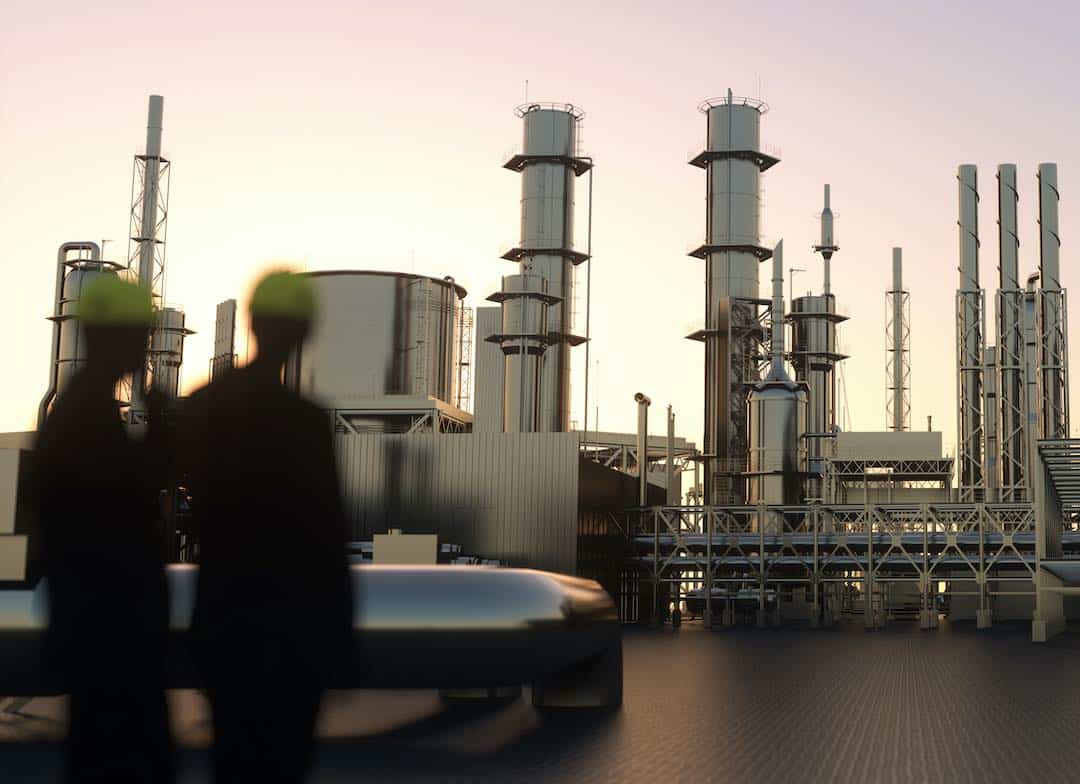
Dramatic decrease in environmental impacts of European chlorine production
Thanks to new energy mixes developed in many European countries and a complete switch to the membrane electrolysis process, the environmental impacts of the production of chlorine have been dramatically reduced in Europe during the last decade.
According to the latest Eco-profile, the Global Warming Potential impact in 2020 has been reduced by 22.3 % since 2011. Thanks to the high chlorine content in PVC (57%), these improvements automatically reduce the environmental impacts for PVC.
Further, PVC production processes have been continually improved in recent years and their environmental impact steadily reduced. The European PVC industry recognises that, along with all other manufacturing industries, it must pursue continual environmental improvement.

PVC requires less feedstock energy than other materials
According to the eco-profile data published by Plastics Europe for general purpose plastics, there is no remarkable difference in the process energy from extraction of oil to plastic production between PVC and the other polymers.
PVC, of which more than half of its weight is composed of common salt, requires about half the feedstock energy needed for the polymers based mainly on hydrocarbons such as LDPE, HDPE, and PP. The sum of process energy and feedstock energy for suspension PVC is therefore only about 60 MJ/kg, below the corresponding sum for those other polymers.